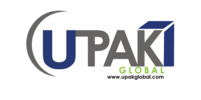
Media
General Description |
The U-Track C is a print and inspect flexible module specially designed for primary package serialization process that required flexibility to handle wide/heavy product and that frequently is used to serialized printed labels that are applied to cartons. This unit provides an ultimate solution since is small and portable equipment for the packaging operations that intends to serialize products in more than one packaging line. This off-the-shelf machine provides everything required for the utmost control and safety on the serialization process, even the most demanding operation will find all its requirements met by the FCG2. The UTRACK FCG2 offers a viable option for the entire pharmaceutical industry, including the CMOs. Ultimate Solutions and Systech have defined, integrated, and tested this unit to provide fast delivery, reduce deployment risks and control in-project engineering costs. This solution has an integrated user interface that allows the user to navigate the Systech and machine controls alarms from the same environment. The UTRACK FCG2 is backed by Systech and UPAK services and support teams for expert deployment and ongoing support. Applications:
|
|
Machine Highlights | Portable compact design | |
Enclosed and secured serialization process | ||
Audible and visible alarms | ||
Interface access levels | ||
Serialization ready | ||
Ergonomically designed | ||
Multi size folded carton | ||
Overall Machine Footprint | Length (A): 1524.00 mm - 60" Depth (B): 1022.35 mm - 40 1/4" Height (C): 1816.10 mm - 71 1/2" Conveyor Height: 939.80 mm - 37" |
|
Machine Flow Direction | Left to right or Right to Left | |
|
Carton Dimensions: L(dimension parallel to movement)-W-H • Minimum: 50.8 mm x 25.4 mm x 12.7 mm [2" x 1" x 1/2"] • Maximum: 203.2 mm x 203.2 mm x 152.4 mm [8" x 8" x 6" ] |
|
Output | Up to 180 cpm Automated Feeding Up to 20 cpm Manual Feeding (maximum speed dictated by operator) |
|
Utility Requirements | Voltage: 1 phase (5 wires) 120 VAC ±10% - 60Hz | |
Amps: 30 amps | ||
Air: 75 PSI on 3/8” ID tube – 1 cfm | ||
Noise: <75 DB | ||
Safety | Upak Part Number (UPN):FC-G2-01A ISO 13849-1:2006 Category 3 safety compliant | |
Structural System | Upak Part Number (UPN):FC-G2-02A Stainless steel frame 2" X 2", stainless steel and anodized aluminum construction |
|
Feeding System | UPN-FC-G2-05B Side Belt Infeed | |
Conveyor System | UPN-FC-G2-04D Flat belt conveyor with belt speed up to 100 ft/min. Anodized aluminum construction and urethane white endless belt | |
Machine Covers | UPN-FC-G2-03A - Front opening upper cover UPN-FC-G2-03C - Interlock for upper side cover |
|
Product Guides | UPN-FC-G2-06C - Side guides with quick adjustment and position feedback | |
|
UPN-FC-G2-08E - VideoJet M600 OEM TIJ • Side B • Encoder |
|
|
• Data Matrix Minimum Module Size: 0.25 x 0.25 mm • Data Matrix Symbol Size: 16x16 to 26x26 • 1D Barcode Thin-Bar Width (min): 0.167 mm • Text Character Height: 1.30 mm |
|
Inspection Brackets | Camera mounting with Y and Z quick adjustment and position feedback | |
Printer Brackets | Printer mounting with Y and Z quick adjustment and position feedback | |
Reject Systems | Lockable reject station Air blow off carton ejection Manual regulation for blow off eject pressure adjustment |
|
Electrical Panel | Stainless steel panel with main power disconnect | |
HMI | SS HMI enclosure with service ports Avantech computer 15" monitor USB and ethernet ports |
|
PLC Allen Bradley CompactLogix | High-speed counter modules | |
Combination of digital and analog counter integrated | ||
Controller tasks | ||
Built-in communications ports | ||
Ethernet/ IP node | ||
Access to DeviceNet network | ||
Embedded I/O modules | ||
Network | Stratix 2000 switch, unmanaged, 8 copper ports | |
Control Panel Push Buttons | Start – To start the system | |
Stop – To stop the system | ||
Reset/Acknowledge- To reset/remove an alarm or fail condition on the control panel and to acknowledge an alarm. | ||
Safety Reset - To reset safety circuit after an Estop event and to reset safety circuit after a guard door open. | ||
Emergency Stop - One (1) illuminated red, twist-‘n’-release emergency stop pushbutton and to shut off power to the U-Track system. | ||
Sensors | Photo switch Photoelectric Sensors (Tracking Sensors, Reject Verify, Reject Bin Presence) | |
Pressure Switch Sensors (Compress Air Low) | ||
Optical Fork Sensors (Printer Trigger, Camera Trigger, Reject Station) | ||
Fail Safe | All electrical components fail safe hardwire and programmed | |
Power Failure Condition | In the event of a power failure, the operator must remove all the cartons inside the machine. Once the machine is cleared, the system can be re-started following the normal procedure. | |
Operation with disabled Vision Inspection System | Operation of the machine with a disabled Vision Inspection System can only be initiated by personnel with Administrator level, which will disable the Vision Inspection System from the Systech HMI. When this is done, the entire machine control is transferred to the machine’s HMI. Start of a new lot is done from the machine HMI. Once the cartons leave the printing station, they continue their travel directly to the Good Product area unless an alternate alarm occurs. | |
Operation with disabled Printer | Operation of the machine with a disabled printer can only be initiated by personnel with Supervisor or above level, which will disable the printer from the machine HMI. The machine can be run using pre-printed cartons. In this condition, the Printer Trigger Sensor is disabled and the cartons continue their travel to the Systech Vision Inspection Station where they are inspected following the normal system sequence. | |
E-Stop Condition | In the event the machine is stopped using the E-Stop button, the system’s safety circuit release all source of energy of the machine and brings them to a safe condition. In this situation, the cartons correct alignment on the conveyor is compromised. Once the E-Stop is deactivated, alarms and products cleared, the machine can be re-started. | |
Critical and Non Critical Alarms | The U-Track alarms will be programmed in the U-Track PLC and will be managed from the HMI. Alarms will indicate any abnormal condition and guarantee an operator action | |
Documentation |
|
|
(Internal QC Check) |
This document will include basic machine function testing that will includes IO’s, wiring check, alarm testing and a 5 min run for the class and product selected by the client. Documentation will be executed following GAMP 5 compliance. | |
Language | English | |
Media | Hard copy binder with a disk containing the electronic manual |